Productivity – Why to Switch from Pieces Counting to SAM ?
/ Industrial Engineering /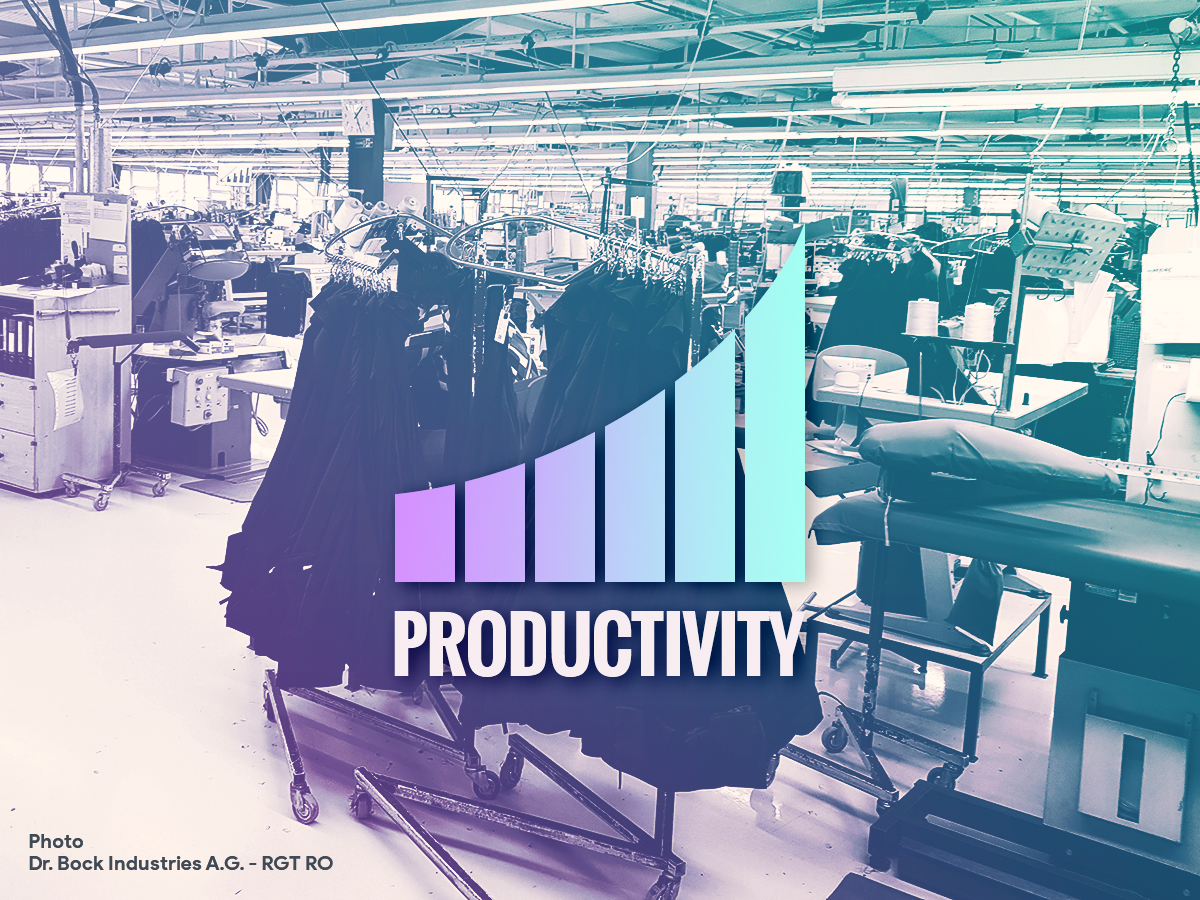
Sales, market share, profit margin are the well known and frequently used indicators by the management.
What is common ? All of them are out of control of the management, are external indicators.
The mass production belongs to the past and the cost and price competitiveness made the differences, the productivity – as internal indicator, under control and influence – could measure the company growth.
As productivity definition should be understand the quantitative and qualitative results of the input of all resources.
Simple : what kind and how much resources I need to get ready the product (with the required quality) ?
The scope is clear : minimizing the resources. This includes the Lean concept to eliminate the wastes, the Kaizen concept for continuous improvement and my I say our vision too, the World with fair concern to the resources.
“Measure it to improve it” – paraphrasing Lord Kelvin – measure the results and together with it measure the resources used to get the results.
Measure and improve from the start of the company and continuously, not only when the dark clouds are already on the horizon, that could be to late.
The well-known 3M defines the necessary resources for the readymade garment : Material + Machine + Man.
In the CM based RMG factory the “Material” is a given thing, no influence on it. In case of full product, the situation is similar but is packed better.
In practice the company could have influence on the productivity by the availability of the equipment’s and the quality of the workers.
A healthy productivity improvement means the existence of a balance between the investments in equipment and investment in the quality of the human resources.
Increasing the productivity with new and performant equipment is a bought productivity – already embedded. It could be necessary time by time, but its fee is the highest, requires large investments.
Investment in the human resources by competencies development, knowledge transfer, trainings, workplaces engineering means to create the productivity. This is the challenging field for the IE (Industrial Engineers).
Looking around about the deployment of the RMG industry that perfectly indicates the expectations of the brands and buyers: create the productivity. Otherwise the equipment’s are available in their places, why to have such a logistics costs, plus the stress generated by the set of unpredictable values of the variables regarding quality, quantity and delivery time ?
The best formal expression regarding how to improve productivity is given by S. Sakamoto:
Productivity = Method x Performance x Utilization
Improving any of the three parameters will result in improved productivity.
Only the last parameter (Utilization) includes the machines but this parameter is influenced by the applied Methods.
Method
Means motion patterns, organization and training. Could provide motivation and could increase the Utilization too.
Developing standard methods, reducing the work content and defining the SAM (features provided by timeSSD® ) contributes to the methods improvements.
The right method development makes the tasks distributable among operators.
The key parameters of the line balancing are the right competences (workers) in the right places assuring the bottleneck free flows.
Performance
Reflects the motivation of the worker and is measured against the standards with the efficiency formula: (Engineered standard time) / (Used time for the execution).
Training, control, incentives and instruction of the workers improves the performances.
Utilization
Measured by (Time used for creating value) / (Planned work time of the equipment). It could be influenced by the applied methods as part of the performed workplace engineering.
The condition of the equipment, the knowledge level of the maintenance team, the production planning and control are the musts for this parameter’s improvement.
An equivalent formula is:
Productivity = Effectiveness x Efficiency x Management
The best approach of it is coming from Peter Drucker: “Efficiency is doing things right, effectiveness is doing the right things.”
With the above complete and simple statement, the Productivity improvement tasks are defined by default :
• Analysis of the work content
• Measure the performances against standards
• Perform the production planning
The accent is on the work content analysis, with common words, on the “work study”.
This process is systematic both in the investigation and in the development of the solution and it’s the most penetrating available tool.
It includes both the “Method study” and “Time study” (or “Work measurement”) processes.
With the “Method study” the operations are examined in small details and the improvements are applied where is necessary. All steps, motions are documented for further use in time study and operator trainings.
As results the operations are simplified and the safety and working conditions are improved.
Together with the “Time study”, which provides the SAM, are the most accurate tools to settings standard of performance.
The “Time study” provides accurate basis for productivity monitoring, resource planning, line balancing, target times for appraisal, scheduling, capacity planning and labor cost forecast.
The work study results should be applied to produce the productivity improvements. The workers training, the continuous activity tracking, control and feedback are part of the improvement process which requires new practices in the company.
The widely used Productivity indicator is: (Number of output pieces) / (Number of workers participating).
In general, could be accepted – together with the necessary attention for the days when the styles are changing – if the scope is to have the productivity curve of the individual or of the line.
Unfortunately, this indicator can’t be used to compare any lines between them or to provide any reference with the exterior.
The updated Productivity formula is: ((Number of output pieces) x (SAM of the manufactured product)) / (Number of workers participating to manufacture)
The same logic should be applied in case of the WIP (Work In Progress) indicator which has the today’s widely accepted formula of : (Input pieces) – (Output pieces).
The updated WIP indicator’s formula is : (Input pieces) x (SAM of the product) – (Output pieces) x (SAM of the product). The WIP data in this format could be easily transformed to show the duration (expressed for example in number of shifts) for which the groups and lines has sufficient products to work.
Case study
The GPD – shop floor control software developed by DataS – manages tens of RMG companies’ manufacturing activity.
Analyzing the productivity indicators, it seems that in the companies where are not applied the accurate work study the updated Productivity indicator is higher with 10% – 15% comparing with the companies where the Method and Time studies are normal, accurate, daily practices.
Having the occasion to perform work studies, for evaluation scopes, in few of this “leader” companies, for evaluation purposes, the reality shows frightening figures which are less with 30% – 35% comparing with the used ones in the decision process. The evaluations were done in Romanian manufacturing units and a (not surprising) particularity is that the larger the factory, the bigger is the illusion.
These “leader” companies, with reputation, completely neglect the “Utilization” factor as the “off standard” related, missing, data collection shows.
Most likely will follow the abandon of the operators activity related data collection combined with the profit figures swooping. The rest is just question of time, without return.
To support the productivity increase of the small and big manufacturers in the RMG sector we provide, by experienced professionals, the work measurement services as part of our BPO and consulting activity.
We can work :
• remotely based on tech-packs and additional data, using as tool and data transfer support the timeSSD® software
• on-site, based on request